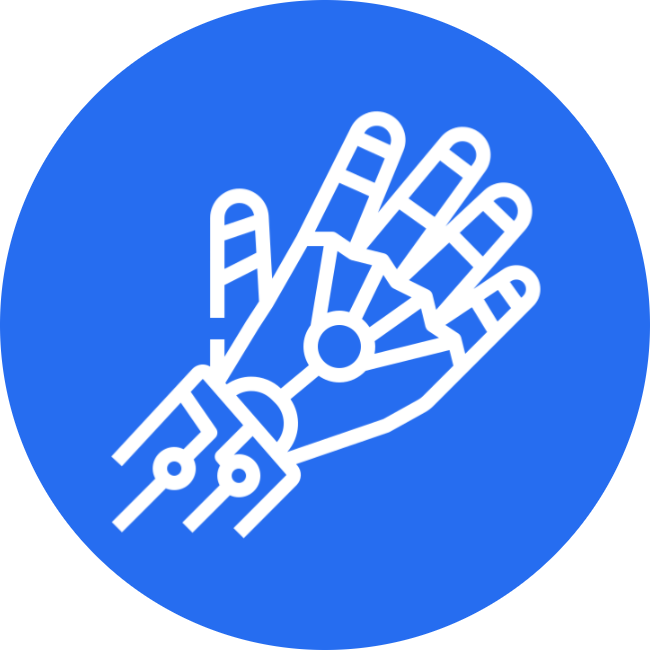
Problem: The client required the development of a prototype mechanical manipulator (master-slave) for use in mobile chemical-biological laboratories. The client needed a mechanical manipulator (master-slave) that operated without an electrical power source.
Objective: Develop and create an analog of a robotic master-slave manipulator using budget-friendly and readily available components, without compromising the precision and quality of manipulation. This involves finding and using economical alternatives to expensive components, ensuring high precision in movements, and maintaining all functional capabilities of the original system. The primary goal is to ensure that the robotic manipulator, assembled from inexpensive materials, can perform tasks with the same degree of accuracy and reliability without using electricity, suitable for mobile chemical-biological laboratories.
Proposal: A 3D prototype of a master-slave mechanical manipulator was developed. After the digital version was approved, a physical prototype was printed using a 3D printer. This prototype functioned exclusively by utilizing conventional mechanical principles without electricity. The developed prototype eliminates the need for electric drives, sensors, and complex electronic systems, enhancing the reliability and safety of the device in operational and field conditions. After testing, the 3D prototype of the mechanical manipulator effectively performed its functions while maintaining high precision and control over operations.
Market Advantages: Unlike its electronic counterparts, this mechanical manipulator has several significant advantages. Firstly, it is more accessible, as its design relies on simple and widely available mechanical components such as levers, pulleys, cables, and springs, which are easy to find and replace. This significantly reduces the cost of the device and its maintenance. Additionally, the mechanical manipulator is easy to repair. Since it does not contain complex electronic systems and sensors, maintenance and repair can be conducted without the need for specialized equipment and highly skilled personnel. Any malfunctions can be quickly detected and fixed even in field conditions, significantly reducing downtime and increasing the device's reliability.
Solution: For transferring manipulations in our mechanical manipulator, we used a cable system. This system allows for high precision and reliability in controlling the actuating elements. In the design of the cable system, one end of the cable is securely attached to the operator's control arm, while the other end is attached to the manipulator's actuating arm. Moreover, the cable system allows the manipulator to be used in environments where electronics might be unreliable or where there is no access to electricity. This makes our manipulator ideal for extreme or remote conditions, such as deep-sea research, space missions, or areas with high radiation levels. It is important to note that the mechanical design of the manipulator is carefully thought out and executed to ensure high precision and control over all movements. Precise mechanical connections and quality materials allow the manipulator to perform tasks with the same accuracy as its electronic counterparts, making it an ideal solution for use in various conditions where access to electricity is limited or nonexistent. Thus, the master-slave mechanical manipulator combines affordability, ease of repair, and high precision, offering an effective and reliable solution for a wide range of tasks.
Objective: Develop and create an analog of a robotic master-slave manipulator using budget-friendly and readily available components, without compromising the precision and quality of manipulation. This involves finding and using economical alternatives to expensive components, ensuring high precision in movements, and maintaining all functional capabilities of the original system. The primary goal is to ensure that the robotic manipulator, assembled from inexpensive materials, can perform tasks with the same degree of accuracy and reliability without using electricity, suitable for mobile chemical-biological laboratories.
Proposal: A 3D prototype of a master-slave mechanical manipulator was developed. After the digital version was approved, a physical prototype was printed using a 3D printer. This prototype functioned exclusively by utilizing conventional mechanical principles without electricity. The developed prototype eliminates the need for electric drives, sensors, and complex electronic systems, enhancing the reliability and safety of the device in operational and field conditions. After testing, the 3D prototype of the mechanical manipulator effectively performed its functions while maintaining high precision and control over operations.
Market Advantages: Unlike its electronic counterparts, this mechanical manipulator has several significant advantages. Firstly, it is more accessible, as its design relies on simple and widely available mechanical components such as levers, pulleys, cables, and springs, which are easy to find and replace. This significantly reduces the cost of the device and its maintenance. Additionally, the mechanical manipulator is easy to repair. Since it does not contain complex electronic systems and sensors, maintenance and repair can be conducted without the need for specialized equipment and highly skilled personnel. Any malfunctions can be quickly detected and fixed even in field conditions, significantly reducing downtime and increasing the device's reliability.
Solution: For transferring manipulations in our mechanical manipulator, we used a cable system. This system allows for high precision and reliability in controlling the actuating elements. In the design of the cable system, one end of the cable is securely attached to the operator's control arm, while the other end is attached to the manipulator's actuating arm. Moreover, the cable system allows the manipulator to be used in environments where electronics might be unreliable or where there is no access to electricity. This makes our manipulator ideal for extreme or remote conditions, such as deep-sea research, space missions, or areas with high radiation levels. It is important to note that the mechanical design of the manipulator is carefully thought out and executed to ensure high precision and control over all movements. Precise mechanical connections and quality materials allow the manipulator to perform tasks with the same accuracy as its electronic counterparts, making it an ideal solution for use in various conditions where access to electricity is limited or nonexistent. Thus, the master-slave mechanical manipulator combines affordability, ease of repair, and high precision, offering an effective and reliable solution for a wide range of tasks.